-
Precision Sheet Metal Fabrication
-
Stainless Steel Sheet Metal Fabrication
-
Sheet Metal Stamping
-
Automotive Sheet Metal Components
-
Medical Equipment Parts
-
Sheet Metal Assembly
-
Plastic Injection Molding
-
Sheet Metal Forming
-
Sheet Metal Welding
-
Metal Laser Cutting
-
Sheet Metal Bending
-
Sheet Metal Powder Coating
-
Custom Metal Fabrication
-
Custom Plastic Molding
-
Customized Metal Bracket
-
Custom Metal Enclosures
-
Windmill Parts
Automobile Industry Stamping Piercing Process Fine Blanking Parts Progressive Die
Place of Origin | Nantong,CHINA |
---|---|
Brand Name | Strong,OEM or ODM |
Certification | ISO 13485, CE Marking, UL Certification, SO9001, IATF-16949, ISO-3834, ISO-14001, customer specified certificate, etc. |
Model Number | Auto-15 |
Minimum Order Quantity | 20000+ PCS |
Price | USD 0.1~50/PCS |
Packaging Details | Pearl cotton, foam, wrapping tape, carton, cardboard, pallet, etc. |
Delivery Time | About 30-35 working days |
Payment Terms | L/C, D/A, D/P, T/T, Western Union, MoneyGram |
Supply Ability | 80000 pcs/month |
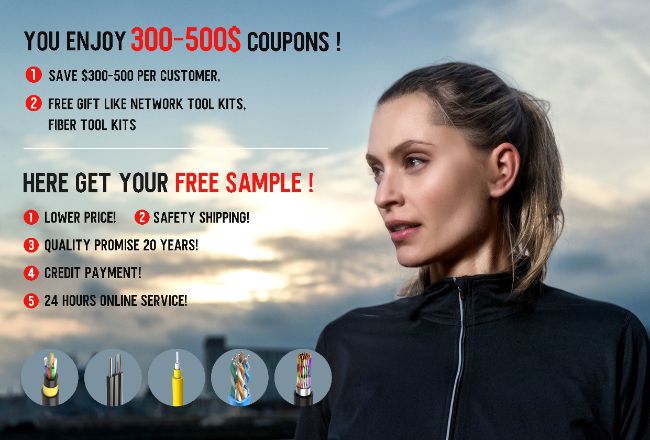
Contact me for free samples and coupons.
Whatsapp:0086 18588475571
Wechat: 0086 18588475571
Skype: sales10@aixton.com
If you have any concern, we provide 24-hour online help.
xName | Piercing Process Fine Blanking Parts | Size | According To 2D&3D Drawings |
---|---|---|---|
Color | According To 2D&3D Drawings | Tolerance | According To Customer Requirements |
Application | Engine Components;Transmission Systems;Brake Systems;Suspension Systems;Fuel System Components;Exhaust System Components | Thickness | Customized; According To 2D&3D Drawings |
Shape | Customized; According To 2D&3D Drawings | Material | Steel, Stainless Steel, Aluminum, Or Other Alloys. |
Process | The Manufacturing Process Used For Producing The Fine Blanking Parts, Which Involves Precision Blanking, Shearing, And Forming Operations. | Surface Treatment | The Surface Finish Or Treatment Applied To The Fine Blanking Parts, Such As Polishing, Plating, Coating, Or Painting, To Enhance Their Appearance And Protect Against Corrosion. |
Highlight | Metallic Fine Blanking Die,Stamping Piercing Process Fine blanking,Fine Blanking Parts Progressive Die |
1.Introduction——Piercing Process Fine Blanking Parts
We are excited to introduce our state-of-the-art Automobile Industry Stamping Piercing Process Fine Blanking Parts Progressive Die. This cutting-edge solution is specifically engineered for the automotive industry, offering high-quality fine blanking parts with exceptional precision and reliability. With our customer-centric approach, we take pride in providing OEM (Original Equipment Manufacturer) as well as ODM (Original Design Manufacturer) services, ensuring customized solutions that cater to the unique requirements of our customers.
Usage:
Our Automobile Industry Stamping Piercing Process Fine Blanking Parts Progressive Die finds extensive use in the automotive industry for various applications. These fine blanking parts are employed in critical areas such as body panels, brackets, fasteners, and electrical components. They play a vital role in ensuring structural integrity, assembly compatibility, and overall performance of automotive systems. The accuracy and consistency of our progressive die-produced parts contribute to the quality, durability, and safety of automobiles.
Production Materials:
We utilize a wide range of high-quality materials that are carefully selected to meet the demanding requirements of the automotive industry. These materials include various grades of steel, alloy metals, and specialized materials with excellent strength, corrosion resistance, and formability. Our material selection ensures that the fine blanking parts produced using our progressive die exhibit superior performance and longevity in challenging automotive environments.
Production Process:
Our Automobile Industry Stamping Piercing Process Fine Blanking Parts Progressive Die is manufactured using advanced production techniques and cutting-edge machinery. The production process involves precision tooling, piercing, stamping, and forming operations. Our skilled engineers and technicians meticulously design and manufacture the progressive die to ensure precise and efficient production of fine blanking parts. With stringent quality control measures at every stage, we ensure that each component meets the highest standards of dimensional accuracy and surface finish.
Market Situation:
The market demand for Automobile Industry Stamping Piercing Process Fine Blanking Parts Progressive Die is experiencing significant growth due to the automotive industry's constant pursuit of higher performance and advanced technologies. As manufacturers strive for lightweighting, energy efficiency, and safety enhancements, the demand for fine blanking parts produced with progressive die technology continues to rise. Our company closely monitors market trends and invests in cutting-edge technologies to stay at the forefront of the industry. We are well-prepared to meet the evolving demands and deliver innovative solutions to our customers.
OEM and ODM Services:
We are proud to offer comprehensive OEM and ODM services to our valued customers. Our experienced team of engineers and designers works closely with clients to understand their specific requirements, design preferences, and industry standards. Whether it involves modifying existing designs or developing custom Automobile Industry Stamping Piercing Process Fine Blanking Parts Progressive Die from scratch, we possess the expertise and capabilities to deliver tailored solutions. Our OEM and ODM services ensure that our customers receive high-quality products that perfectly align with their brand, applications, and manufacturing processes.
In conclusion, our Automobile Industry Stamping Piercing Process Fine Blanking Parts Progressive Die offers advanced solutions for the automotive industry. With our commitment to customer satisfaction and the ability to provide OEM and ODM services, we are dedicated to meeting the diverse needs of our customers. Contact us today to discuss your specific requirements and experience the excellence of our progressive die-produced fine blanking parts. Together, we can achieve superior performance, reliability, and success in automotive component manufacturing.
2.Product parameters:
Piercing Process Fine Blanking Parts | |||
Size | Customized; According to drawings | ||
Color | Metallic, Black; According to customer requirements | ||
Material | The type of material used for the fine blanking parts, such as steel, stainless steel, aluminum, or other alloys. | ||
Process | The manufacturing process used for producing the fine blanking parts, which involves precision blanking, shearing, and forming operations. | ||
Tolerance | According to drawings and customer requirements. | ||
Surface Treatment | The surface finish or treatment applied to the fine blanking parts, such as polishing, plating, coating, or painting, to enhance their appearance and protect against corrosion. | ||
Application | Engine Components;Transmission Systems;Brake Systems;Suspension Systems;Fuel System Components;Exhaust System Components | ||
Thickness | Customized; According to drawings | ||
Shape | The specific shape or geometry of the fine blanking parts, which can range from simple to complex profiles, depending on the application requirements. | ||
Mold making time | 25 working days | ||
Delivery date | About 30-35 working days | ||
Certification | Any relevant certifications or standards that the fine blanking parts comply with, such as ISO, ASME, or industry-specific certifications. | ||
Price | Need to negotiate between buyer and seller | ||
Packaging Details | Box/foam/pearl cotton/carton/tray/customized | ||
Supply Ability | 10000 pcs/month | ||
Payment Terms | L/C, D/A, D/P, T/T, Western Union, MoneyGram | ||
Highlights | Any specific features or characteristics of the fine blanking parts that make them stand out or provide a competitive advantage, such as high precision, tight tolerances, or unique design elements. Please note that the parameter list may vary depending on the specific requirements of the fine blanking parts and the industry they are used in. |
3.Our advantage:
1) Five production branches
A total of 5 factories in China and Vietnam maintain a stable supply chain for customers;
2) Sign a non-disclosure agreement
We keep your ideas and designs completely confidential;
3) Comprehensive production line
Sheet metal stamping and injection molded parts are comprehensive. We have our own assembly line, paint line, one-stop service;
4) Experienced business development team
We have 15 business development experts with good English ability and communication skills to keep abreast of your needs;
5) We have a professional engineering team
Half of them have more than 15 years of experience in the mold industry, especially in molds, forming products, sheet metal products, stamping products and injection molding products;
6) We are an innovative company
We actively develop the Internet, medical equipment, aerospace, new energy storage, automobile and other industries, and develop the latest technology to meet the high production requirements of customers;
7) Fast delivery time
We have advanced technical processing machines and time-mobilized personnel, so we can complete prototype projects within 3-5 days, prototype molds within 15 days, and mass-produce complex molds within 3-5 weeks;
8) Quality control experts
We have passed ISO9001 quality management system certification, and can even apply for certificates for various quality products according to customer needs. On-site material, tool and part inspection before production and delivery.
4.Our factory
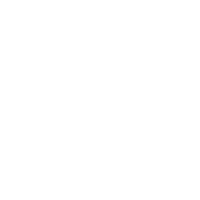
Shanghai Strong Metal Production was established in June 2003 with a total registered capital of 67 million yuan and a total construction area of 30,000 square meters. There are 5 factories in total, located in Nantong, Taicang, Nanjing, Vietnam and Shanghai.
The main products of our factory are OEM and ODM metal and plastic manufacturing services. Focusing on metal manufacturing, it has comprehensive capabilities such as independent mold design, metal stamping, sheet metal, laser cutting, powder coating, welding, and injection molding.
The company has more than 500 employees and more than 40 engineers, including engineering engineers, drafting engineers, quality engineers, process engineers, etc. engineer. We can provide services from drawings to samples and batches, and 24-hour technical support.
We have many advanced production equipment: more than 50 punching machines (up to 1000 tons), more than 20 injection molding machines (up to 740 tons), more than 20 bending machines (up to 600 tons), more than 20 automatic welding arms, more than 50 Welding table, 8+ laser cutting machine, 400m powder spraying line, etc. In terms of QC testing tools, we have CMM, two-dimensional measuring instrument, hardness tester, etc. (contact us if you need it, and we will provide you with a list of related equipment )
In 2021, Shanghai Strong Metal Production's annual turnover has exceeded 200 million yuan. We will continue to find and provide customers with better solutions, create more value, and create a better world.
5.Our production line
6.Certificate
7.FAQ
Q: Are you trading company or manufacturer?
A: We are original manufacturer. We can do OEM/ODM business.
Q: How long is your delivery time?
A: General delivery time:30 days.
Q: What is your terms of payment?
A: T/T 50% as deposit, and 50% before delivery. To be discussed.
Q: How to buy your products?
A: You can buy the products from our company directly. Normally the procedure is sign the contract, payment by T/T, contact the shipping company to delivery the goods to your country.
Q: What is the warranty?
A: The free warranty is one year from the day of Commissioning qualified. If there is any fault for our products within the free warranty period, we will repair it and change the fault assembly for free.